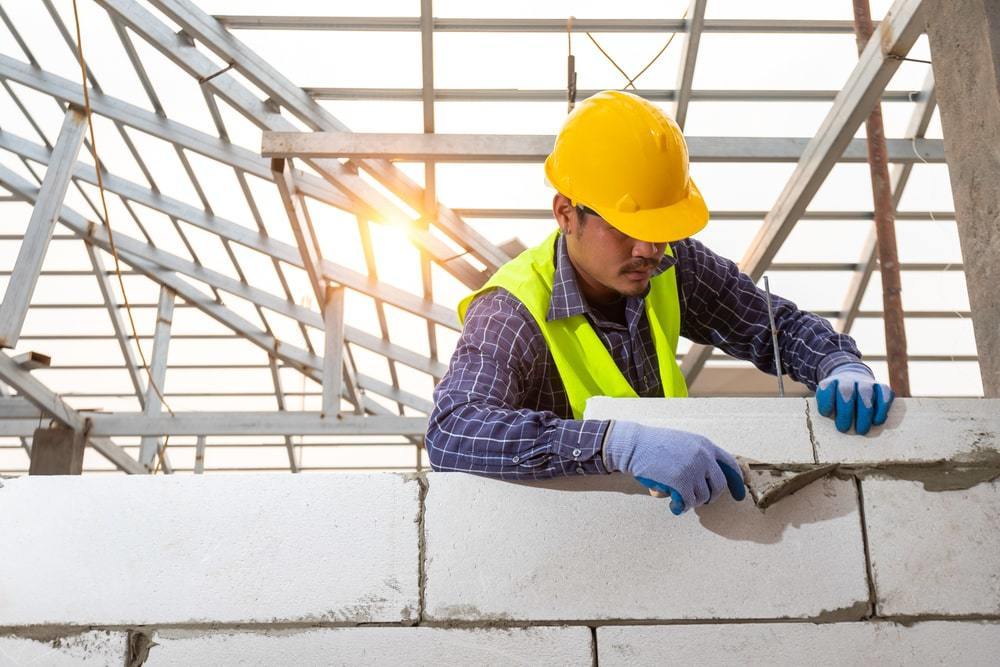
Autoclaved Aerated Concrete (AAC) is a precast, foam concrete building material that is lightweight and ideal for constructing blocks-like concrete masonry units. The materials that makeup AAC products are quartz sand (SiO2 with impurities), calcined calcium sulfate, lime (CaO), cement, water, and aluminum powder which are cured in an autoclave under high heat and pressure.
AAC products can be used for both interior and exterior construction. To protect them from the weather, they can be painted, coated with stucco or plaster, or covered with siding materials like veneer brick or vinyl siding. AAC materials may be quickly and easily installed and can also be routed, sanded, or cut to size using common power tools and carbon steel cutters.
Evolution of AAC Blocks
AAC was developed by Swedish architect and inventor Dr. Johan Axel Eriksson, in the middle of the 20th century while working with Professor Henrik Kreuger at the Royal Institute of Technology. The method was granted a patent in 1924. Eriksson’s accomplishment immediately sparked the necessary business interest, and in 1929, a factory in Sweden. In 1940, the name “Yxhult” was changed to “YTONG” because it was simpler to say. The business CarlsroKalkbrukSkovde began manufacturing AAC blocks in 1932, and the product was given the trade name Durox. In 1934, a significant rival emerged that began producing AAC blocks under the trade name Siporit (as of 1937, Siporex).
With the advent of technology licensing and knowledge transfer, AAC manufacturing went global in 1937. After World War II, there were only a few key manufacturers of AAC technology: Hebel, Siporex, and Ytong, along with Durox. All of them were successful in selling AAC technology licenses during the 20th century while also helping to advance AAC production, product quality, and its applications through yearly conventions.
After World War II, Germany, the United Kingdom, Sweden, Denmark, and the Netherlands established themselves as the major AAC centers, despite the fact that countries used various technologies to create similar goods. In the 1980s, due to the struggling domestic market, the influence of Swedes gradually decreased, which led to a reduction in Siporex activities and the absence of new factories since the 1990s. Additionally, the Germans also took over and expanded upon the Ytong knowledge that the Swedes had developed in the 1980s, and multiple plants based on different technologies were realized in Asia, the Middle East, and Eastern Europe.
At the start of the 1990s, the first AAC plant based on tilt-cake technology(Ytong) was delivered to China. Since then, there has been a significant outflow of technology, and as of 2014, there are more than 3,000 AAC production facilities, with an estimated annual production capacity of 450 million m3 of non-reinforced blocks. While Western European, Australian, Japanese, and Korean markets are increasingly focusing on reinforced panels and high precision blocks, mass production of blocks is still popular in Central and Eastern Europe and India.