Company Broacher
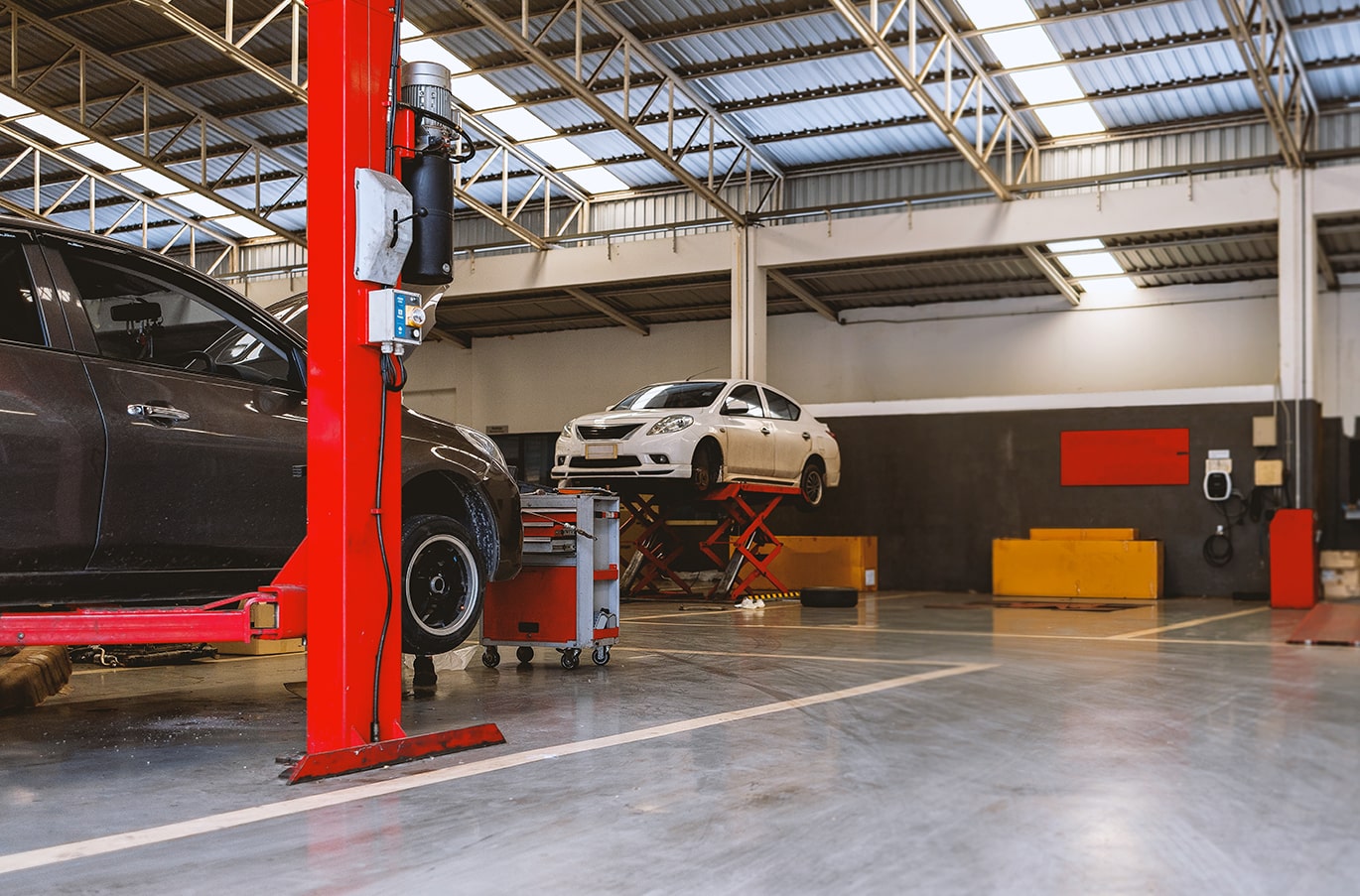
Buses
The glass processing market for buses essentially consists of two very different products – windshields and sidelites. Each has their own challenges and opportunities. Bus windshields need to be bent and annealed, whereas bus sidelites need to undergo a process to be bent and tempered.
Both types of bus glass require exceptional processing quality and capability.
“That’s because the newest trends coming to the bus glass market include cut-outs, digital and screen printing, larger surfaces and thinner glass to reduce weight and fuel consumption. Yet all of this adds up to glass that is much more difficult to heat treat. As a processor, you need to sharpen your expertise to be able to deliver – but the rewards are well worth the effort.”
The growing shapes of things to come
Not all sidelites are growing in size necessarily, but bus designs in general are looking at larger glass surfaces as the de-facto standard. Large and continuous transparent glass surfaces add finesse to the bus design and allow passengers to indulge more in the passing scenery.
Earlier, maximum glass requirements were 2.4 x 1.5 m. Today, bus glass of 2.4 x 1.7 is becoming the new standard. Those bus glass processors who are prepared to serve these needs are much better positioned to take advantage of this growing market trend.
Growing continuous glass surfaces are being requested for both sidelites and windshields. In the past, the windshield of a city bus would extend to the top only. Now, tourist buses in particular are requiring windshields that continue on the top of the bus to add flamboyance and a wow-effect for sightseers.
Digital and screen-printed glass surfaces are used to hide the structural elements of the bus. These surfaces block the unsightly metal or cords and add to the aesthetical appeal of the vehicle.
QUALITY SYSTEMS AND QUALITY ASSURANCE